What is Selective Laser Sintering (SLS) 3D Printing? Understanding Its Basics
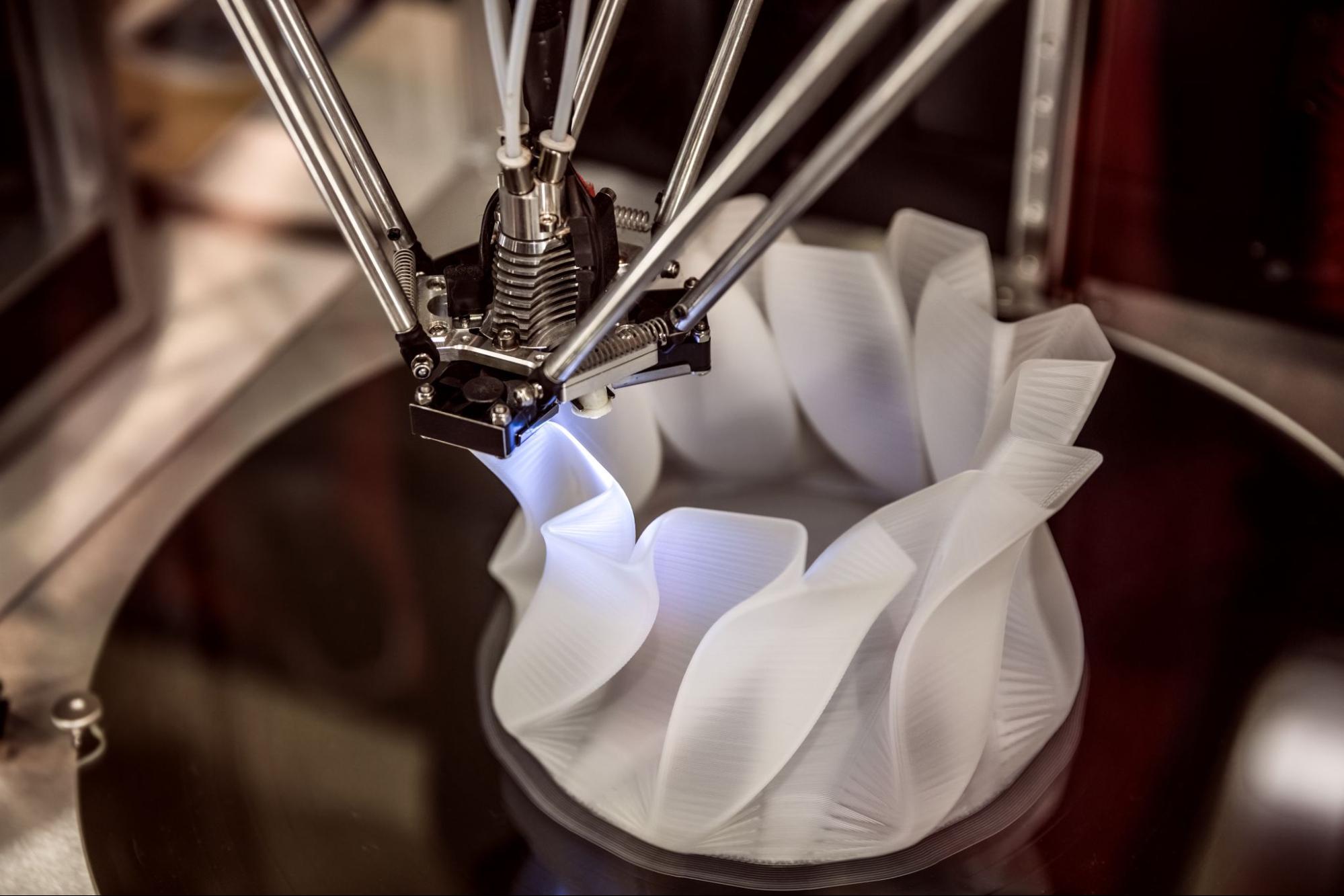
Selective Laser Sintering (SLS) is a powerful 3D printing technology used for producing durable and highly detailed parts. It’s widely used in industries like aerospace, automotive, healthcare, and manufacturing due to its ability to create strong, functional components. But what exactly is SLS 3D printing, and how does it work? Let’s break it down in a way that’s easy to understand.
On This Page
- What is Selective Laser Sintering (SLS) 3D Printing?
- How Does Selective Laser Sintering (SLS) 3D Printing Work?
- Advantages of SLS 3D Printing
- Challenges in SLS 3D Printing
- Common Applications of SLS 3D Printing
- SLS 3D Printing vs. Other 3D Printing Methods
- Fab Lab in the Philippines
What is Selective Laser Sintering (SLS) 3D Printing?
SLS 3D printing is an additive manufacturing process that uses a high-powered laser to selectively fuse powdered material layer by layer to create solid objects. This technology is known for producing strong, detailed, and functional parts without the need for support structures, making it ideal for industrial applications.
How Does Selective Laser Sintering (SLS) 3D Printing Work?
Unlike other 3D printing methods like FDM (Fused Deposition Modeling) or SLA (Stereolithography), SLS doesn’t require support structures since the unsintered powder acts as a natural support. Here’s a step-by-step look at the process:
1. Preparing the 3D Model
Before printing begins, a 3D model is designed using CAD (Computer-Aided Design) software. The file is then sliced into thin layers to guide the printer.
2. Layering the Powder
A thin layer of powdered material—usually nylon, but sometimes metal or composite materials—is spread across the build platform.
3. Laser Sintering
A laser precisely fuses the powdered material in the desired pattern, solidifying it into a thin cross-section of the object. The process is repeated layer by layer until the part is complete.
4. Cooling and Post-Processing
Once the printing is done, the part needs to cool down before being removed from the powder bed. Excess powder is brushed off, and the part may undergo additional finishing processes like dyeing, polishing, or coating.
Advantages of SLS 3D Printing
SLS technology offers several benefits that make it a popular choice for businesses and engineers looking for high-quality 3D-printed parts.
1. No Need for Support Structures
Since the unused powder supports the object during printing, SLS eliminates the need for additional support structures. This results in more design freedom and less post-processing work.
2. Strong and Functional Parts
SLS parts are highly durable and resistant to wear and tear, making them ideal for mechanical applications. The materials used, like nylon and thermoplastics, provide excellent strength and flexibility.
3. High Detail and Complex Geometries
SLS allows for intricate designs and complex geometries that would be difficult to achieve with traditional manufacturing methods. This is perfect for industries requiring precision, such as aerospace and medical devices.
4. Efficient for Batch Production
Compared to FDM or SLA, SLS can produce multiple parts in a single print cycle. This makes it a great option for short-run production and prototyping.
Challenges in SLS 3D Printing
While SLS 3D printing offers many advantages, it also comes with certain challenges that users need to consider.
1. High Initial Cost
SLS printers and materials tend to be more expensive compared to FDM or SLA, making them less viable for small businesses and hobbyists.
2. Post-Processing Requirements
Although SLS does not require support structures, printed parts still need post-processing, such as powder removal and surface finishing, to achieve the desired quality.
3. Limited Material Options
While SLS primarily uses nylon and a few other polymers, the material selection is not as vast as some other 3D printing methods, limiting its applications in certain fields.
4. Requires Specialized Knowledge
Operating an SLS printer and optimizing designs for the process requires expertise, making it less beginner-friendly compared to other 3D printing technologies.
Common Applications of SLS 3D Printing
SLS 3D printing is used in various industries due to its reliability and versatility. Here are some key applications:
1. Industrial Prototyping
Companies use SLS for rapid prototyping because it produces highly accurate, functional prototypes that closely resemble final products.
2. Aerospace and Automotive Components
Parts like brackets, ducting, and housings are commonly made with SLS due to their strength and lightweight properties.
3. Medical and Healthcare
SLS is used to create customized prosthetics, surgical guides, and medical implants due to its precision and biocompatible material options.
4. Consumer Products
From eyewear frames to sports equipment, SLS helps manufacturers create strong, lightweight products with complex designs.
SLS 3D Printing vs. Other 3D Printing Methods
If you’re exploring 3D printing in the Philippines, you might be wondering how SLS compares to other technologies. Here’s a quick comparison:
Feature | SLS | FDM | SLA |
Material | Powdered Polymers | Filament (Plastic) | Liquid Resin |
Strength | High | Moderate | Moderate |
Detail | High | Moderate | Very HIgh |
Support Structure | Not Needed | Required | Required |
Cost | Medium to HIgh | Low | Medium |
NOTE: While FDM is more affordable and SLA offers high detail, SLS strikes a balance between strength, precision, and scalability, making it a great choice for industrial applications.
Fab Lab in the Philippines
Another great place to explore SLS 3D printing and other advanced manufacturing technologies is a Fab Lab in the Philippines. These fabrication laboratories provide access to various digital fabrication tools, including 3D printers, CNC machines, and laser cutters. Fab Labs are excellent for startups, students, and innovators who want to experiment with 3D printing without investing in expensive equipment.
Selective Laser Sintering (SLS) 3D printing is a powerful technology that enables the production of strong, detailed, and functional parts without the need for support structures. Its ability to handle complex geometries and batch production makes it ideal for industries like aerospace, healthcare, and manufacturing. If you’re exploring 3D printing in the Philippines, SLS is a great choice for creating durable prototypes and end-use products.
Looking for quality 3D printing in the Philippines? Contact us today to learn more about our products!